When Was the Potter’s Wheel Invented?
One early example of a mechanical device developed by humans is the potter's wheel. The first potter's wheels were slower than the fast wheels developed later.
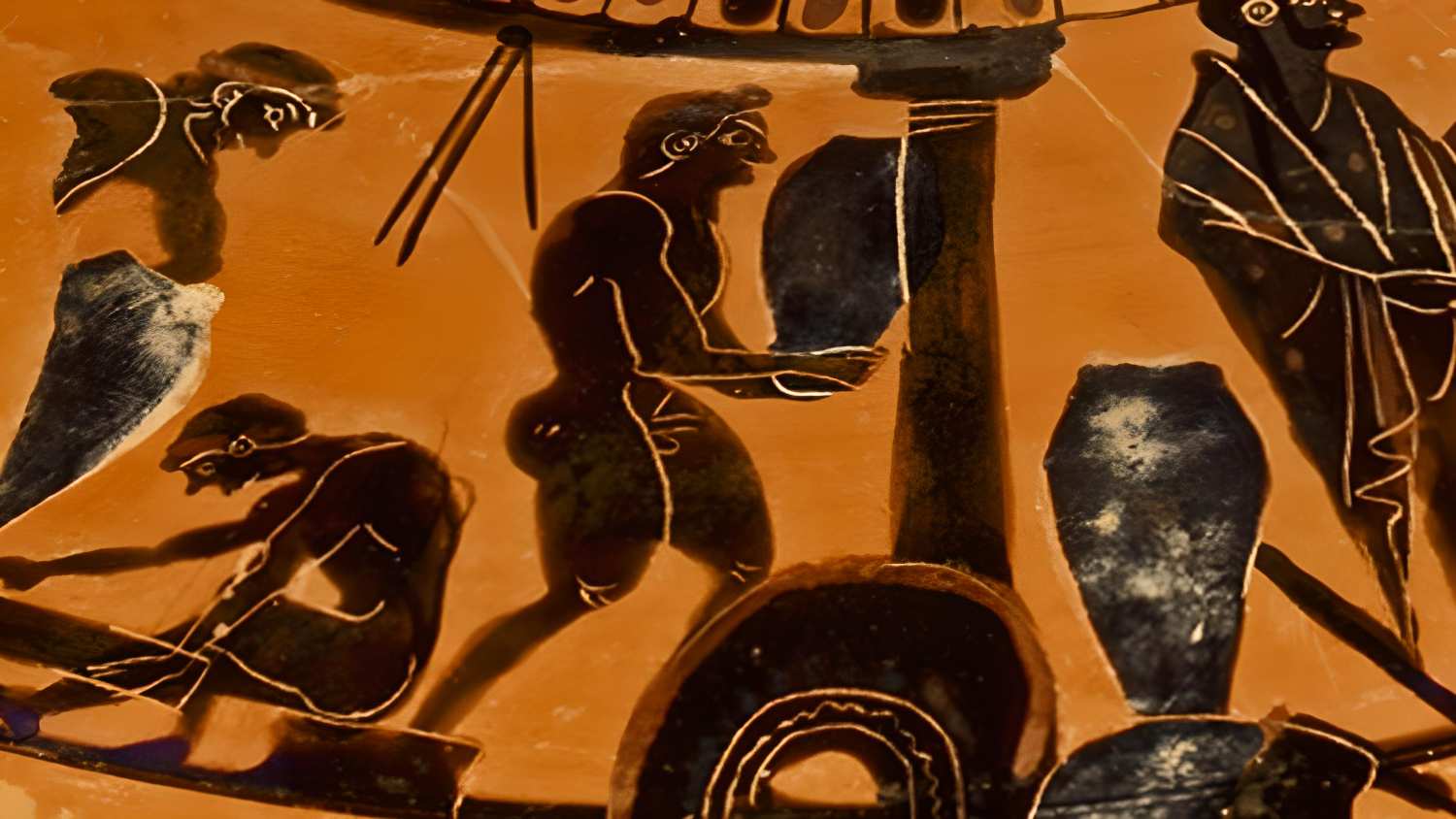
One early example of a mechanical device developed by humans is the potter's wheel. The first potter's wheels were slower than the fast wheels developed later.